Burn-in is a process performed on electronic components before they are put into regular use to detect potential failures and ensure reliability. During this process, a power supply is run through the electronics at an elevated temperature for an extended period, often many hours. This stress testing helps identify and eliminate early-life failures, ensuring that only components that can withstand operational demands are deployed, thereby improving overall product reliability and performance.
Our integrated fixtured cart enables testing of a variety of products, with multiple carts facilitating faster loading and unloading, and cost-effective changeover to new products. Features like high-volume, horizontal airflow ensures optimal product change rates.
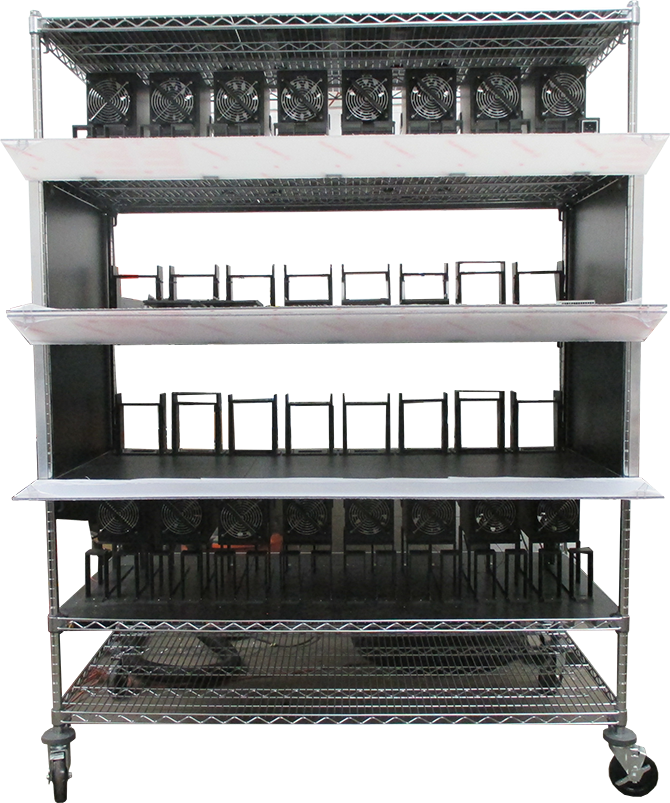
Keypoints to note:
- Process to detect failures and ensure reliability of electronic components
- Conducted before regular use
- Involves running a power supply through the electronics
- Helps identify and eliminate early-life failures
- Ensures components can withstand operational demands
- Improves overall product reliability and performance
Manufacturing and programming such fixtures typically take four to six weeks.
Burn-in Racks and Their Uses
Design Verification
Enhances the efficiency and accuracy of the testing process, allowing test engineers to focus on other critical tasks.
Troubleshooting
Aids engineers in diagnosing problems with faulty power supplies pulled from production or returned from field failures.
Typical Features of Burn-in Racks
Sturdy Construction and Design
Made from durable extruded aluminum and heavy duty caster wheels.
Fast loading and Unloading
Integrated fixtured cart system, which accommodates a variety of products and allows for quick changeovers
Innovative Connectors for Mechanical Loading
Provides a secure and reliable connection that ensures consistent electrical contact during testing. This mechanism simplifies the process of connecting and disconnecting test devices, reducing the time and effort required for setup and minimizing the risk of connection errors
Mirotech manufactures bed of nails test fixtures in the Greater Toronto Area, providing high-quality solutions for efficient and accurate PCB testing.
Your UUT is in safe hands, mechanically
The non-wiping mechanism involves a controlled, uniform, and consistent vertical movement during PCB testing. This ensures that all test points on the PCB are contacted simultaneously and with equal force by the test probes or pogo pins. This uniform contact is critical for the following reasons:
Consistent Test Results: By ensuring that each test point receives the same amount of pressure, the non-wiping mechanism contributes to the accuracy and repeatability of test results. This is crucial for identifying faults and verifying the functionality of the UUT.
Minimizing Wear and Tear: A key feature of the non-wiping action is that the test probes make contact with the test points without sliding across them. This reduces wear and tear on both the probes and the PCB, minimizing the risk of damage. As a result, the lifespan of the test fixture and the UUT is extended, reducing the frequency of replacements and repairs.
Enhanced Reliability: The linear collapse design, which incorporates the non-wiping mechanism, ensures precise alignment and reliable connections during testing. This mechanism maintains the integrity of the contact points, contributing to the overall reliability of the testing process.
Protection of Test Components: By avoiding lateral movement or sliding, the non-wiping mechanism protects sensitive components on the PCB. This is particularly important for high-density boards where test points are closely spaced, and any sliding action could cause shorts or other damage.
In summary, the non-wiping mechanism in UUT test fixture design is essential for maintaining the reliability, precision, and efficiency of the testing process. It ensures high-quality results while protecting both the test fixture and the unit under test, ultimately contributing to more robust and reliable electronic products. Whether using a bed of nails or flying probe testing, the principles of controlled, precise contact are critical for achieving accurate and repeatable test results.
Let’s work together on your
next project
We have been providing our customers with test fixtures for over 20 years. We have a proven track record of providing excellent customer service, quality products, and reasonable prices.