CheckSum test fixtures are essential tools in Automated Testing Equipment (ATE) for evaluating electronic components and assemblies, especially in PCB testing. The core of the CheckSum fixture, where all probes and contacts are located, is custom-made for each Unit Under Test (UUT), ensuring precision and reliability. At MiroTech, we specialize in customizing these fixtures, including bed of nails probing, to meet the specific needs of your UUT, while the rest of the fixture remains standard.
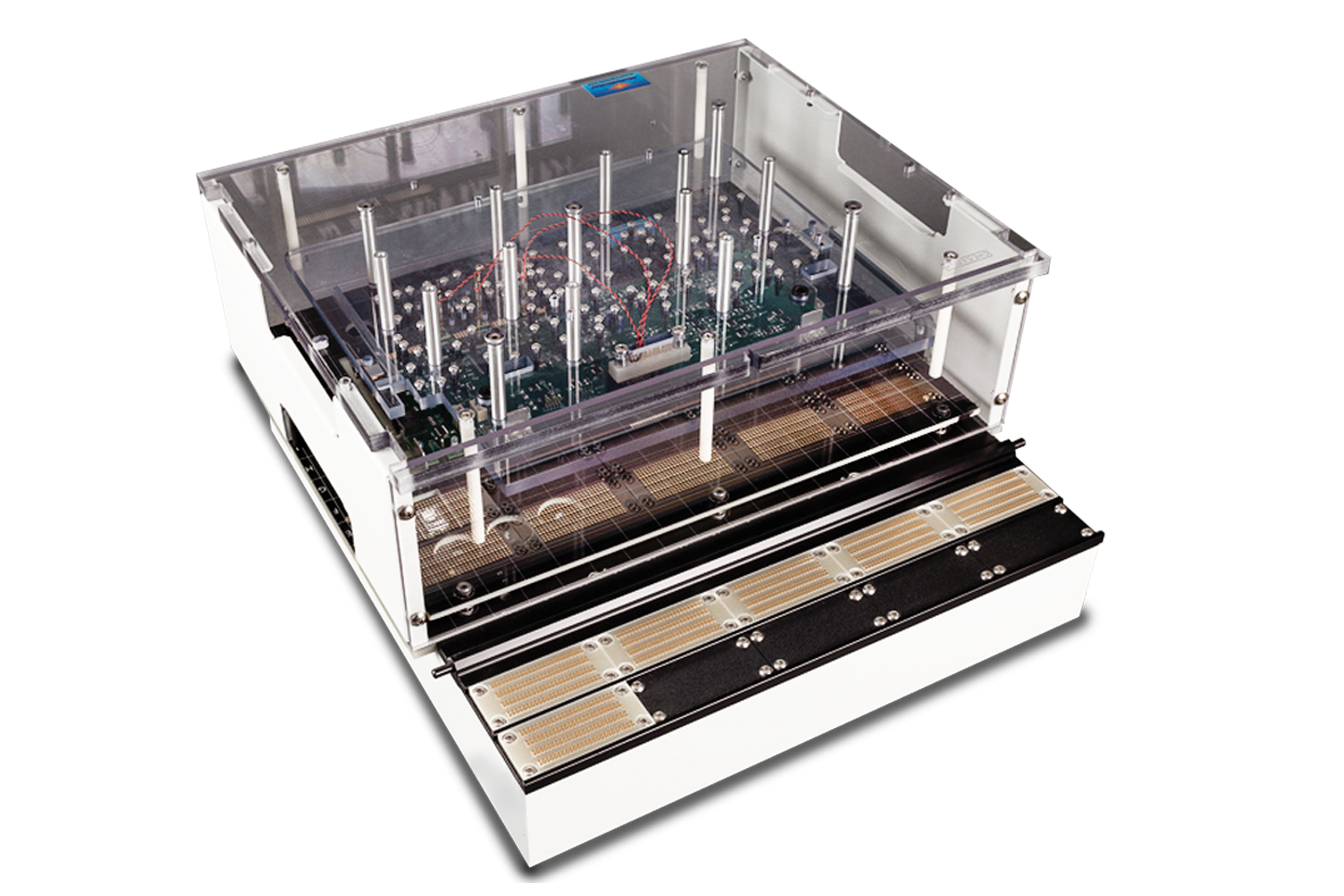
CheckSum System Integration and Mirotech
Using a CheckSum PCB test fixture kit with our service would be beneficial for your testing and product development processes due to its efficiency and reliability. Given our previous experience, we understand the value of precise, automated test fixtures in ensuring product quality and performance. The kits are quickly assembled and tailored to your specific needs, significantly streamlining the test engineer’s development cycle. This rapid setup reduces downtime and accelerates your time-to-market, allowing you to maintain high standards while enhancing productivity and efficiency in your testing procedures.
Keypoints to note:
- Offers efficient and reliable testing solutions, ensuring thorough evaluation of electronic components and assemblies, particularly for PCB testing.
- Leveraging our previous experience, we provide precise, automated test fixtures that guarantee high product quality and performance.
- Quickly assembled and customized to meet your specific needs, significantly streamlining the test engineer’s development cycle and reducing downtime.
- Accelerates your time-to-market and help maintain high standards while boosting productivity and efficiency in your testing procedures.
Manufacturing and programming such fixtures typically take four to six weeks.
Your UUT is in safe hands, mechanically
The non-wiping mechanism involves a controlled, uniform, and consistent vertical movement during PCB testing. This ensures that all test points on the PCB are contacted simultaneously and with equal force by the test probes or pogo pins. This uniform contact is critical for the following reasons:
Consistent Test Results: By ensuring that each test point receives the same amount of pressure, the non-wiping mechanism contributes to the accuracy and repeatability of test results. This is crucial for identifying faults and verifying the functionality of the UUT.
Minimizing Wear and Tear: A key feature of the non-wiping action is that the test probes make contact with the test points without sliding across them. This reduces wear and tear on both the probes and the PCB, minimizing the risk of damage. As a result, the lifespan of the test fixture and the UUT is extended, reducing the frequency of replacements and repairs.
Enhanced Reliability: The linear collapse design, which incorporates the non-wiping mechanism, ensures precise alignment and reliable connections during testing. This mechanism maintains the integrity of the contact points, contributing to the overall reliability of the testing process.
Protection of Test Components: By avoiding lateral movement or sliding, the non-wiping mechanism protects sensitive components on the PCB. This is particularly important for high-density boards where test points are closely spaced, and any sliding action could cause shorts or other damage.
In summary, the non-wiping mechanism in UUT test fixture design is essential for maintaining the reliability, precision, and efficiency of the testing process. It ensures high-quality results while protecting both the test fixture and the unit under test, ultimately contributing to more robust and reliable electronic products. Whether using a bed of nails or flying probe testing, the principles of controlled, precise contact are critical for achieving accurate and repeatable test results.
Let’s work together on your
next project
We have been providing our customers with test fixtures for over 20 years. We have a proven track record of providing excellent customer service, quality products, and reasonable prices.